Important Factors When Selecting A Cutting Tool
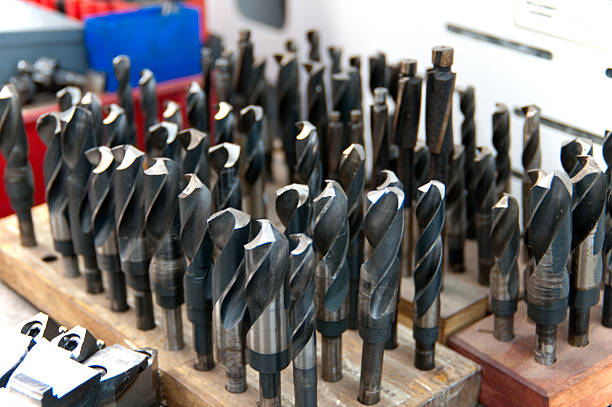
If you are choosing a tool for cutting, you need to consider its material properties and the way it cuts a particular material. Here we will go over the K quality chemical stability, side cutting edge angle and additional factors to consider.
An appropriate cutting tool as a pencil grinder and straight grinder tools will make your life easier and save money while ensuring quality output. Here are a few essential things to consider before choosing tools. Talk to your machine shop about specific equipment if you're uncertain about what you want. If you really want to learn additional information on tool, you have to check here at https://www.sundicuttingtools.com/products/full-solid-cbn-inserts/ website.
1. Material Property
Material properties are essential to different operations of machining. They, like knives, need to withstand temperatures above 100°C without loosing their cutting edge. Also, they need to resist abrasion, adhesion and thermal conductivity.
To get the most out of cutting equipment, these aspects are vital. This article will discuss the characteristics of materials to comprehend the usage as well as the lifespan of cutting equipment.
The life of the cutting tool and its speed are crucial for the production process. The life of the cutting tool is influenced by many factors including feed rate, tool geometry and wear on the tool. The variables that influence tool life will increase productivity.
A quality cutting instrument will endure for hundred of thousands uses. The durability of a tool for cutting will be determined by the speed it has to be able to cut various types of materials. Apart from cutting speeds the cutting tool must have high wear resistance. You must be aware of cutting speeds and feed rates before buying the tool.
2. K Factor
The K-factor of cutting tools defines the design cut edge. The cutting edge's radius is dependent on a number of variables, such as the type of material, machine technique and the type of layer.
The most common method of evaluation is with cutting speeds of around 35 milliseconds. The measurement area along the cutting edge can be seen in Fig. 1. Additionally, the dimensions of Sy and Sa can also affect the size of Sa and Sy affect the force load and heat load.
To determine the K-factor of cutting tools, the tool is made of metal Alumina, metal, and abrasive. The K factor of a tool is determined by the contact length a and the inclination g. When the angle of rake g increases, the objective roughness function also increases.
The more roughness is the of the objective, the more intricate the materials are. An increase in the K factor indicates that the cutting tool is not working properly.
3. Chemical Stability
Cut-off tools that are made of cubic boron nitride (CBN) are among the most complex material. They are also high-temperature resistant and possess outstanding thermal stability. They can be classified into the categories of high-c-BN or low-c BN. Low-cBN equipment does not contain CBN in any way, and high-cBN models contain 75-95 volume% of boron Nitride and metallic binders.
Though greasy oil is among the most common cutting fluid, it's other characteristics are not remarkable. They're expensive, and emit a significant amount of smoke, making their use unsuitable for contemporary production. E-PE additives and mineral oils can be mixed to make greasy oils low viscosity. The result is excellent lubricity as well as a longer time of life for tools.
4. Side Cutting Edge Angle
The angle at which the back rake is determined is the cutting edge of the tool's cut side angle. The angle is measured between the face of the cutting tool and the perpendicular plane. The tip of the tool is positive when it is sloped down but negative if the slope is up.
In general, the back rake angle will range from between 5 and 15 degrees. This angle is essential to know when creating and fabricating a tool.
The rake of a cutting tool is determined by the angle formed between the surface of the tool as well as the line that runs parallel to the base of the tool. This angle helps reduce friction between the tools and the workpiece. This can result in more compact, better chips.
Positive rake angles reduce the strength of the cutting edge segment as well as reduce the capacity of heat transfer by the tool. Therefore, positive rake angles are more suitable for metals with a high strength and alloys that are tough, whereas the negative angles work best for soft metals or those that are brittle.
5. High Yield Strength At Operating Temperature
High yield strength is one of the most popular features that is present in HSS tools. However, in this type of cutting device, the edge is loaded close to the limit of its yield strength, leading to severe adhesive wear.
Cutting materials that are chemically tough will result in increased wear. HSS tools are also susceptible to having a sharp edge due to friction. This article examines the factors that affect yield of cutting tools.
The temperature at which an instrument is the main factor that determines the amount of heat generated by the tool. The temperature at which the tool that is used for cutting grows with the speed of cutting and the temperature of the work material is affected by the quantity of heat that is flowing through the machine.
This effect is particularly prominent with intermittent cutting. Operating temperature is a key factor in the lifespan of a tool and its performance. In order to prolong the life of the tool and decrease heat generated it is necessary for the tool to to cut at a specific temperature.
6. Tool Material
High-temperature tool hardness determines the material's ability to resist heat, avoid plastic deformation and retain toughness even in extremely hot temperatures. This property also determines its wear resistance.
The tool's capacity to withstand the cutting process is determined on its stability in thermal heat. Its temperature will be lower when cutting if it has higher thermal conductivity. It is essential to select materials that are able to handle the high speed of cutting.
The quality of cutting tool material is crucial for industrial processes. It affects the amount of material removed, the quality of the surface, the precision, and the cost for the maker.
Final Words
Manufacturers can reduce scrap, boost production and improve the quality of parts by selecting suitable tool material. This ensures the long-term success of its operation. To choose the right tool material, a manufacturer must first consider the exact needs of the cutting application.